Table Of Content
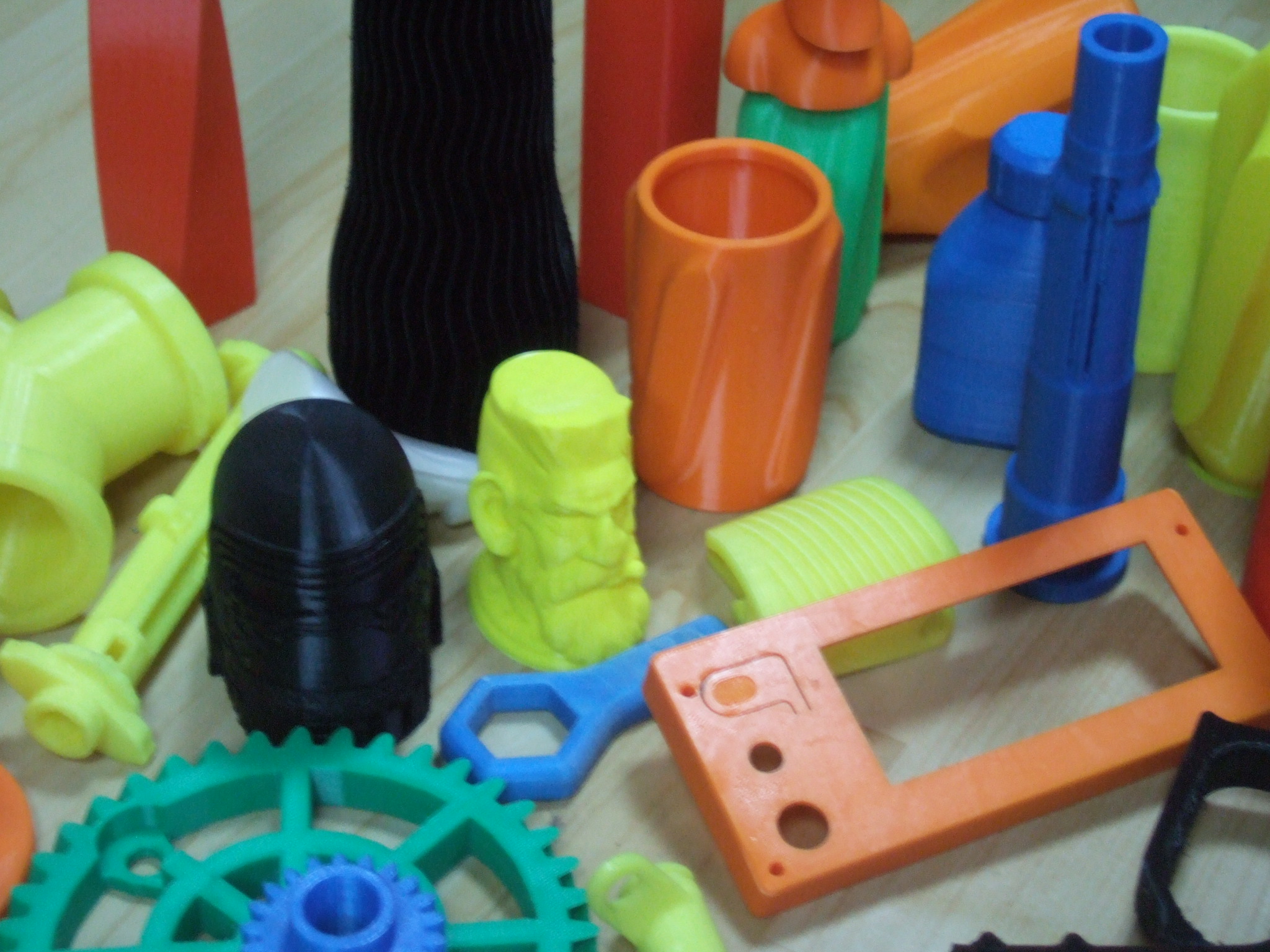
By identifying the type of product, we can know at which stages of the process savings can be made based on its existence and materials. Bear in mind that with an existent study and analysis of the product, it is easier to start designing. Also, a lack of storability can cause difficulties and increase the costs of distribution.
Reinforcing Rib Structure Design in Plastic Parts
We’re are sure that our team at Martin’s can provide all the guidance you need. WHOD design presents Debris, a balance tower game crafted from upcycled ocean plastic waste, transforming the traditional stacking game into a metaphor for environmental disruption caused by accumulating trash. This innovative approach not only fosters communal enjoyment but also prompts players to engage with marine environmental issues. Plastic Design, Inc. has successfully completed many plastic design and engineering projects for clients in a variety of industries.
Ombak chair consists of 2000 plastic bags salvaged from Bali's rivers - Dezeen
Ombak chair consists of 2000 plastic bags salvaged from Bali's rivers.
Posted: Mon, 08 Apr 2024 07:00:00 GMT [source]
Plastic Part Design Guidelines for Injection Molding Plastic Parts
Despite high upfront costs for tooling and setup, some manufacturing processes produce parts that are inexpensive per unit. Finding the right wall thickness is a key design challenge in many components. It involves balancing lighter weight against functional strength and molding performance. There are multiple factors which are critical to design walls that will perform in use, including mold flow behavior, fiber orientation and correct functional thicknesses. Undercuts can be used to carry out complex forms of molding, such as the overmolding process and the insert-molding process.
This inclusively designed electric mobility vehicle is Tony Stark’s hoverboard
These materials add elegance to your packaging or display and create a higher perceived value in the marketplace. We're able to form 70 mil high-impact polystyrene, 6-1/2 inches deep and greater for larger, taller display trays and specialty applications. We can also form and inline cut large clamshells for products requiring a deep shell. Star Plastic specializes in custom thermoforming of blisters, clamshells, tray and tray lids to precise customer specifications.

It works with other approaches for optimization of design like designing for functionality, assembly, and sustainability, each of which is discussed further, below. Integrated Design Systems (IDS) has a 40-year history of delivering world-class plastic part design and has been the leader in the plastics industry. Our plastics design and manufacturing expertise are based on Michael Paloian’s plastics materials, plastic injection mold design, and plastic product design. He has been a contributing author to plastics textbooks, written hundreds of articles, and lectured throughout the world on plastics design.
The designers and engineers at API have over 250 combined years of experience in designing parts for plastic injection molding, selecting materials, and processing resins (specializing in engineering and high performance resins). This guide was designed to demonstrate the basic elements of proper plastic part design. If different thicknesses of sections are required, make sure the transition is as smooth as possible to make the material flow evenly inside the cavity. This ensures the entire mold will be completely filled, lowering the possibility of defects..
We know that taking the most of the budget for new projects is not always easy. Here are a couple of suggestions for efficient budget management to anticipate events, reduce failures, and control some variations that cause more expenses. Designing a functional industrial product is not the same as an item of design furniture where the important thing is the aesthetics and originality.
One way to overcome the problems that can arise with thick walls is by the addition of ribbing, which increases rigidity while allowing wall thickness to be reduced. Getting ribs right can improve strength and reduce weight, but it can be a process of trial-and-error to find the right rib dimensions, positioning and materials. The idea behind coring out is to simply remove material from a plastic part, leaving a distinct rib structure behind. Ribs not only provide structural integrity to the part but also provide mating surfaces for other parts in the assembly if needed. Other advantages of coring out a part are reduced weight and production time and therefore cost. Leaving ribs in the right location or direction, particularly in bending, will maintain strength throughout the part and improve cosmetics.
Using our voice to build a circular plastic economy - Unilever
Using our voice to build a circular plastic economy.
Posted: Fri, 19 Apr 2024 10:44:23 GMT [source]
Plastics Engineering Major
Please see our basic resin guide for a few examples of commodity and engineering resins that API has become an expert in molding. Use our expertise in industrial product design and engineering to develop plastic products. We offer exceptional project management, fixed budgets,and game-changing designs that could result in higher sales and better brand recognition for your company. Do your pieces have complex internal features or strict tolerance requirements? Depending on the geometry of the design, the production choices may be minimal or require a significant design for manufacturing optimization to make them economical to manufacture. The recommended minimum distance between two ribs is two times of nominal wall thickness.
According to your request, I will put my highest effort into providing you with the best outcome possible. I would make sure that I don't just deliver you the design but an experience that you'll enjoy and remember. Call us for your next plastic forming & plastic fabrication OEM parts requirements in California. Custom thermoforming in California offering regular, thin forming, large formed parts and heavy gauge plastic thermoforming and plastic fabricating of any item, part, component in plastic from prototype to production. Therefore when the thick-section yields, it leads to warping, twisting, shrinkage, or void formation in molded part. When molten plastic passes into the variable cross-section injection mold, the thin plastic section starts cooling first.
This comprehensive service is truly a single source solution for custom biomed and pharmaceutical research equipment. Senior Design Engineer in MNCAdvanced skills in product design.Proficient in surfacing, Solid, and plastics. Plastic Design Products is a trusted leader in setting the scope in the vacuum forming plastic and thermo forming plastic industry in achieving the best in customer service, quality and delivery. We are located in Southern California for easy delivery of your extremely large applications and huge plastic formed parts. To avoid thick sections, uniform wall thickness throughout a part (if possible) is essential.
It depends on the product, the number of pieces to be produced, and the secondary processes (assembly, finishing, and packaging). I am a CAD Designer with more than 5 years of work experience.My design work consists of concept designing, product designing, rendering, reverse engineering, prototyping, mold designing and product manufacturing. I have partnered with molders and manufacturers to provide complete product manufacturing solutions. I also cater to automobile industries and ancillaries for Class-A surface models as a freelance consultant. Therefore Boss design in plastic parts should be as per guidelines to ensure boss strength and avoid injection molding defects.
No comments:
Post a Comment